Under the Occupational Safety and Health Administration’s (OSHA) new beryllium standard, employers have until March 10, 2020, to implement engineering controls if they are needed to control beryllium exposure. OSHA has recommended some minimum exposure control strategies for specific operations that involve beryllium. Let’s take a look.
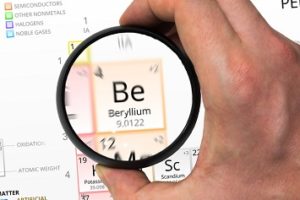
vchal / iStock / Getty Images Plus / Getty Images
Under the new beryllium standard, for each operation in a beryllium work area that releases airborne beryllium, employers must ensure that at least one of the following is in place to reduce airborne exposure:
- Material and/or process substitution;
- Isolation, such as ventilated partial or full enclosures;
- Local exhaust ventilation, such as at the points of operation, material handling, and transfer; or
- Process control, such as wet methods and automation.
OSHA has offered a list of minimum control options that employers could use to comply with this requirement for a number of specific beryllium operations.
Operation: Beryllium oxide forming. For pressing operations:
- Install local exhaust ventilation (LEV) on oxide press tables, oxide feed drum breaks, press tumblers, powder rollers, and die set disassembly stations;
- Enclose the oxide presses; and
- Install mechanical ventilation (make-up air) in processing areas.
For extruding operations:
- Install LEV on extruder powder loading hoods, oxide supply bottles, rod breaking operations, centerless grinders, rod laydown tables, dicing operations, surface grinders, discharge end of extrusion presses;
- Enclose the centerless grinders; and
- Install mechanical ventilation (makeup air) in processing areas.
Operation: Chemical processing, such as leaching, pickling, degreasing, etching, and plating. For medium- and high-gassing operations:
- Perform operation with a hood having a maximum of one open side; and
- Design process so as to minimize spills; if accidental spills occur, perform immediate cleanup.
Operation: Finishing, such as grinding, deburring, sanding, and polishing.
- Perform portable finishing operations in a ventilated hood. The hood should include both downdraft and backdraft ventilation, and have at least two sides and a top.
- Perform stationary finishing operations using a ventilated and enclosed hood at the point of operation. The grinding wheel of the stationary unit should be enclosed and ventilated.
Operation: Furnace operations, such as melting and casting.
- Use LEV on furnaces; pelletizer; arc furnace ingot machine discharge; pellet sampling; arc furnace bins and conveyors; beryllium hydroxide drum dumper and dryer; furnace rebuilding; furnace tool holders; arc furnace tundish and tundish skimming, tundish preheat hood, and tundish cleaning hoods; dross handling equipment and drums; dross recycling; and tool repair station, charge makeup station, oxide screener, product sampling locations, drum changing stations, and drum cleaning stations.
- Use mechanical ventilation (makeup air) in furnace building.
Operation: Machining.
- Use LEV consistent with ACGIH® ventilation guidelines on deburring hoods, wet surface grinder enclosures, belt sanding hoods, and electrical discharge machines (for operations such as polishing, lapping, and buffing);
- Use high-velocity, low-volume hoods or ventilated enclosures on lathes, vertical mills, CNC mills, and tool grinding operations;
- Use LEV on lapping, dicing, and laser cutting for beryllium oxide ceramics; and
- Use wet methods (e.g., coolants).
Operation: Mechanical processing.
- Enclose and ventilate sources of emission;
- Prohibit open handling of materials; and
- Use mechanical ventilation (makeup air) in processing areas.
Operation: Metal forming.
- For rolling operations, install LEV on mill stands and reels such that a hood extends the length of the mill;
- For point and chamfer operations, install LEV hoods at both ends of the rod;
- For annealing operations, provide an inert atmosphere for annealing furnaces, and LEV hoods at entry and exit points;
- For swaging operations, install LEV on the cutting head;
- For drawing, straightening, and extruding operations, install LEV at entry and exit points; and
- For all metal forming operations, install mechanical ventilation (makeup air) for processing areas.
Operation: Welding.
For fixed welding operations:
- Enclose work locations around the source of fume generation, and use local exhaust ventilation; and
- Install close capture hood enclosure designed so as to minimize fume emissions from the enclosed welding operation.
For manual operations:
- Use portable local exhaust and general ventilation.