What tools are you using to reduce work-related injuries and fatalities in your workplace? Do you collect and review your injury and illness data? Review safety bulletins from your industry trade group? Investigate near misses and incorporate lessons learned into your training? But have you ever considered … working cooperatively with your industry competitors? Or with the Occupational Safety and Health Administration (OSHA)? Well, why not?
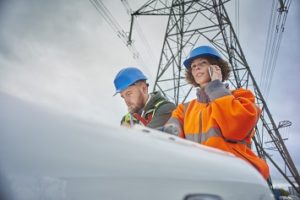
sturti / E+ / Getty Images
Yesterday we looked at the organization and structure of one of OSHA’s longstanding national partnerships, the Electrical Transmission & Distribution (ET&D) Partnership. The cooperation between OSHA, employers, unions, and industry groups has helped to reduce injury and fatality rates in the industry, including a dramatic reduction in fatalities caused by electrocution from contact, from a high of 11 in 2004 to just 1 in 2013.
Here’s a look at the goals and outcomes of the ET&D Partnership.
Partnership Goals
Before a partnership can accomplish anything, it must have goals. The goals of the ET&D partnership provide a characteristic example of the types of goals that OSHA’s strategic partnerships work toward. ET&D partnership’s goals included:
- Collecting and analyzing data to establish causes of fatalities, injuries, and illnesses for electrical work in the industry
- Developing industry best practices and evaluating their effectiveness in reducing fatalities, injuries, and illnesses in the industry
- Ensuring that the partners’ employees were effectively trained to follow safety and health rules, to utilize the established best practices, and to change safety culture
- Improving the safety and health culture within the industry through communication
Products of the Cooperative Effort
Most partnerships result in the production of an assortment of helpful tools that are applicable to their industry. The ET&D Partnership, for example, produced training courses, best practices, and communication tools.
Training courses. The ET&D Partnership developed two courses on the OSHA 10-hour model—a 10-hour course and a 20-hour course—covering industry-specific topics. The 10-hour course is available to all line workers through IBEW training centers. The 20-hour course is specifically designed for foremen, general foremen, and field supervisors. In addition, the partnership developed course materials that can be used as quarterly refreshers. Other partnerships have developed other types of materials, including training videos.
Best practices. A detailed “best practices” document is now available through the partnership that lists not only the “best practice” recommendation but also its benefits and any additional documentation that is available (for example, National Electrical Safety Code standards).
Communication tools. The ET&D partnership developed three specific communication tools for use in the industry:
- A partnership safety video that encourages all employers in the industry to commit to providing a safe and healthy workplace
- A best practices mobile app, released in 2016, that puts the identified best practices at workers’ fingertips
- A national Electrical Safety Stand Down, first observed in 2012, that encourages workers to participate in safety education activities each year
For employers looking for cooperative strategies for improving health and safety in their own facility, as well as raising the standard within their industry, the ET&D Partnership provides an example of how the program can work to the advantage of all concerned groups.