Laboratories need EHS management systems, just like any business does. To help them create a comprehensive system that works for a lab, the National Research Council (U.S.) Committee on Prudent Practices in the Laboratory publication has provided guidance in its “Prudent Practices in the Laboratory: Handling and Management of Chemical Hazards.”
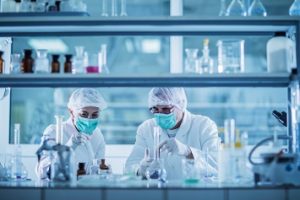
BraunS / E+ / Getty Images
Here’s a look at the Council’s recommendations for implementing, auditing, and maintaining a laboratory EHS management system.
Implementing an EHS Management System
Yesterday we looked at the policy creation and planning stages of a laboratory EHS management system. Once the policy is in place and the planning stage is complete, the program must be implemented successfully. Successful implementation is accomplished through the use of:
- Effective communication strategies linking management, employees, and the public. Internal communication can help to ensure that the system covers everything it needs to cover, without gaps, and also that it does not include things that are not relevant to the organization—like information on radioisotopes in a lab that does not handle them.
- Effective training strategies for EHS at all levels of the organization. Encourage workers to suggest or request training that they may find beneficial.
- A document control system, which is critical to both communications and recordkeeping.
- Effective contingency plans that will enable the lab to respond appropriately and quickly to accidents and emergencies.
Continuously Improving an EHS Management System
Every piece of equipment in your laboratory requires regular maintenance to ensure that it is in good working order. A management system requires regular maintenance, too, in the form of performance measurement, audits, and management of change.
- Performance measurement lets you know how your system is functioning in practice. It will help you to determine whether you are making progress toward your goals and areas where you need to improve.
- Audits provide an in-depth critical evaluation of the EHS management system. They should be conducted by individuals who are competent in the area or activity being evaluated. Plan to follow up on audit findings, both to address problems and to provide recognition.
- Management of change. This is one area in which the EHS management system in a lab may differ markedly from EHS management in other environments. In a lab, changing the various aspects of an experimental process, including scaling it up, happens on a daily basis. In particular, change-related risk assessments and training must address particularly hazardous substances (PHSs), radioisotopes, and infectious agents as needed.
Management Review
The final piece of the EHS management system for laboratories brings matters full circle, with management conducting a periodic review (once a year, at least) of performance measures, audit results, and established goals and objectives. Based on this information, management can decide on goals and objectives for the coming year.