OSHA is expected to revise its Hazard Communication (HazCom) Standard this year to bring it in line with the current Globally Harmonized System (GHS) of Classification and Labeling of Chemicals and formalize various enforcement policies that have been issued since the last major update to HazCom in 2012. Employers that manufacture, import, distribute, or use hazardous chemicals may face additional compliance requirements once the revisions take effect.
GHS is meant to facilitate international trade with a uniform set of chemical labels and standard practices for creating safety data sheets for chemicals in commerce. GHS was agreed to by the United Nations with the goal of adoption of the system in as many countries as possible by 2008. OSHA and other federal agencies have long participated in GHS negotiations. Negotiators have agreed to many changes to GHS since the Third Edition that formed the basis for OSHA’s March 2012 revisions to the HCS.
Although the agency incorporated elements of GHS in a March 2012 rulemaking, those revisions brought the Hazard Communication Standard (HCS) in line with the Third Edition of GHS. However, GHS is a “living document” that is revised about every two years, and the United Nations (UN) just completed the seventh edition. With each revision, the UN has updated what can be included in precautionary statements for various hazards and how such statements should be worded.
OSHA said in the Fall 2018 agenda of regulatory and deregulatory actions that it planned to issue a notice of proposed rulemaking in March 2019 to update the HCS to incorporate elements of the latest edition.
Changes Since Third Edition
The Fourth Edition of GHS included new hazard categories for chemically unstable gases and non-flammable aerosols, as well as further adjustments to the precautionary statements and some clarifications of criteria for precautionary statements to avoid differences in their interpretation.
The Fifth Edition included:
- New test method for oxidizing solids,
- Miscellaneous provisions intended to further clarify the criteria for some hazard classes (skin corrosion/irritation, severe eye damage/irritation, and aerosols);
- Revised and simplified classification and labelling summary tables; and
- New codification system for hazard pictograms.
The Sixth Edition included:
- New hazard class for desensitized explosives;
- New hazard category for pyrophoric gases;
- Miscellaneous provisions intended to clarify the criteria for some hazard classes (explosives, specific target organ toxicity following single exposure, aspiration hazard and hazardous to the aquatic environment);
- Additional information to be included in the Safety Data Sheets; and
- New examples addressing labelling of small packages.
The Seventh Edition includes:
- Revised criteria for categorization of flammable gases within Category 1;
- Miscellaneous amendments intended to clarify the definitions of some health hazard classes;
- Additional guidance to extend the coverage of section 14 of the Safety Data Sheets to all bulk cargoes transported under instruments of the International Maritime Organisation (IMO), regardless of their physical state;
- Revised and further rationalized precautionary statements in Annex 3; and
- New example in Annex 7 addressing labeling of small packages with fold-out labels.
GHS does not require participating agencies to adopt the system “as is,” and OSHA has not yet indicated which elements of the updated GHS it intends to adopt. However, any changes to hazard classifications, SDS requirements, and labeling practices are likely to impact companies that manufacture, import, or distribute hazardous chemicals, as well as all employers whose employees could be exposed to hazardous chemicals on the job. At a minimum, affected employers would need to train their employees on any changes to labels and SDSs and provide information regarding any new hazard classifications that apply to chemicals in use at the workplace.
Formalizing Guidance
According to the entry in the Fall 2018 regulatory agenda, the other goal of OSHA’s HazCom revisions is to “codify a number of enforcement policies that have been issued since the 2012 standard.”
Exactly what that might entail is not yet public. However, since the implementation of the 2012 standard, OSHA has issued a number of directives, letters of interpretation, and memos intended to clarify points of confusion for stakeholders. Many of these would likely form the basis for any revisions to the standard.
Issues addressed in LOIs and other guidance since the implementation of the 2012 standard include:
- Labeling of small packages
- The use of concentration ranges on SDSs
- The use of non-GHS hazard symbols on labels and SDSs
- Information on Hazards Not Otherwise Classified (HNOC) on labels and SDSs
- Classification of flammable and nonflammable aerosols
- Combustible dust hazards
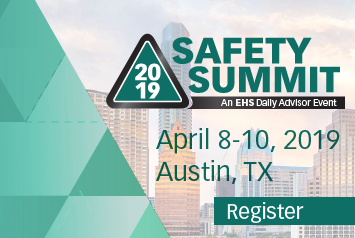
Learn more about fulfilling your compliance obligations and building a strong safety program at Safety Summit 2019 this April!
Takeaways for Employers
Some employers may be tempted to preemptively align their HazCom programs with the Seventh Edition of the GHS; however, this approach can backfire. Not only has OSHA not yet indicated which elements of the Seventh Edition it intends to adopt, but according to OSHA’s 2015 Inspection Procedures for the Hazard Communication Standard, where a later version of the GHS conflicts with the current HazCom standard, employers may be cited with violations if their use of a more recent version of the GHS contradicts or casts doubt on OSHA-required information. For the time being, HazCom 2012 remains the standard by which OSHA will assess employer compliance.
Therefore, the best course of action for employers aiming to prepare for HazCom revisions is simply to focus on compliance with the current standard, which remains the most frequently cited standard in general industry and the second most frequently cited standard across all industries.
Common violations under the current HazCom standard include:
- Failure to develop and implement a written hazard communication program that meets the requirements of the standard
- Failure to provide adequate employee training
- Failure to maintain copies of SDSs for each hazardous chemical and ensure they are readily available to employees
- Failure to train employees on labels and SDSs
- Failure to properly label chemicals in the workplace