Back to Basics is a weekly feature that highlights important but possibly overlooked information that any EHS professional should know. This week, we examine how to use checklists to identify workplace hazards.
As you well know, there are hazards all around you in the workplace. In its Small Business Safety and Health Handbook, the Occupational Safety and Health Administration (OSHA) notes that an effective way to identify workplace hazards is for experienced workers to conduct routine safety and health inspections.
These self-inspections should be conducted routinely by businesses to identify hazards, control identified hazards, and monitor and evaluate hazard controls to verify that they continue to be effective.
OSHA provides several self-inspection checklists in the handbook, designed for general industry workplaces and not construction or maritime industries. They should be used as a starting point for identifying hazards and are based on sources including OSHA standards and generally accepted safety and health principles. The checklists should not be used to assess compliance with the OSH Act or OSHA standards.
Once the checklists are completed, compile information from them with workplace injury and illness records, worker training information, and process and equipment information (e.g., maintenance logs, failure incident reports) to help determine where challenges exist. Find solutions to the challenges using OSHA standards, resources on the OSHA website, and other resources listed in the handbook.
The checklists included in the handbook are not all-inclusive and many not all apply to your business. Topics include posting of required safety and health information, compressed gas cylinders, electrical safety, exit routes and emergency planning, fire protection, hazard communication and chemicals, lockout/tagout procedures, materials handling and storage, personal protective equipment, respiratory protection, and walking-working surfaces.
The first checklist covers Safety and Health Programs:
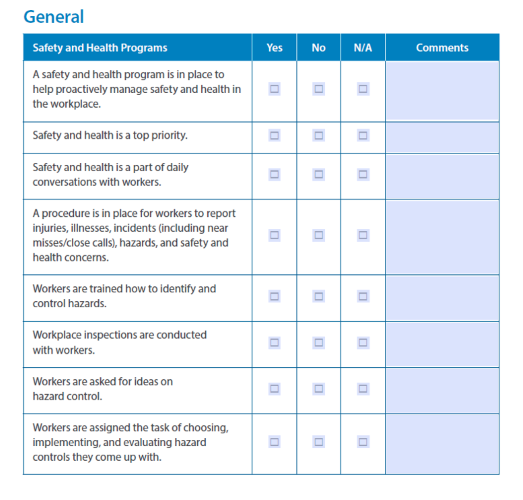
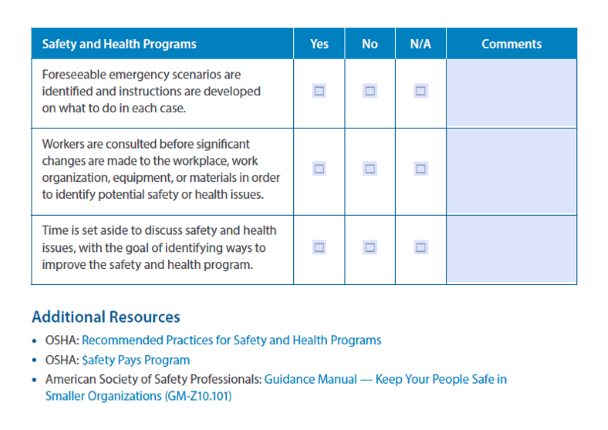